在现代制造业中,聚晶金刚石(PCD)刀具因其卓越的硬度、耐磨性和热稳定性,被广泛应用于加工各种难加工材料,如航空航天复合材料、汽车零部件、3C产品等。然而,要充分发挥PCD刀具的优势,获得高质量的加工效果,合理选择切削参数至关重要。
切削速度
切削速度是影响PCD刀具性能的关键因素之一。适当提高切削速度可以提高加工效率,但过高的速度会导致切削温度急剧上升,使刀具材料的强度和硬度下降,加剧刀具磨损,甚至导致刀尖破损。此外,在高速切削时,机床的振动也会增大,影响加工精度和表面质量。因此,选择合适的切削速度,需综合考虑工件材料、刀具材质、机床性能等因素,以达到最佳的加工效果和刀具寿命。
进给量
进给量的大小直接影响加工效率和表面粗糙度。较大的进给量虽然能提高材料去除率,但会使工件表面残余面积增大,导致表面粗糙度增加,同时也会增加刀具的切削负荷,容易引起刀具崩刃。相反,过小的进给量虽然能降低表面粗糙度,但会使切削温度上升,刀具磨损加剧,降低刀具寿命。因此,合理选择进给量,需要在加工效率和加工质量之间找到平衡点。
切削深度
切削深度的大小对PCD刀具的切削力和切削热有显著影响。增加切削深度可以提高材料去除率,但过大的切削深度会使切削力增大,切削热升高,从而加剧刀具磨损,缩短刀具寿命。此外,切削深度过大还容易引起刀具崩刃,影响加工稳定性。因此,在选择切削深度时,应根据工件材料的硬度、刀具的材质和刃口状态、加工方式等因素进行综合考虑,以确保加工质量和刀具寿命。
总之,切削参数对PCD刀具的性能有着重要影响。合理选择切削速度、进给量和切削深度,不仅能提高加工效率和加工质量,还能延长刀具寿命,降低加工成本。在实际加工中,应根据具体的加工条件和工件材料,不断优化切削参数,以达到最佳的加工效果。
欢迎咨询
上名精工可根据客户不同的加工需求,提供特殊刀具、刀柄、夹具以及非标刀具定制服务,同时还提供PCD刀具激光加工设备。我们专注于为每一位客户量身定制最适宜的刀具加工解决方案,全方位满足您的加工需求,助您降本增效,提高生产效率。
期待与您交流合作,详情欢迎垂询!
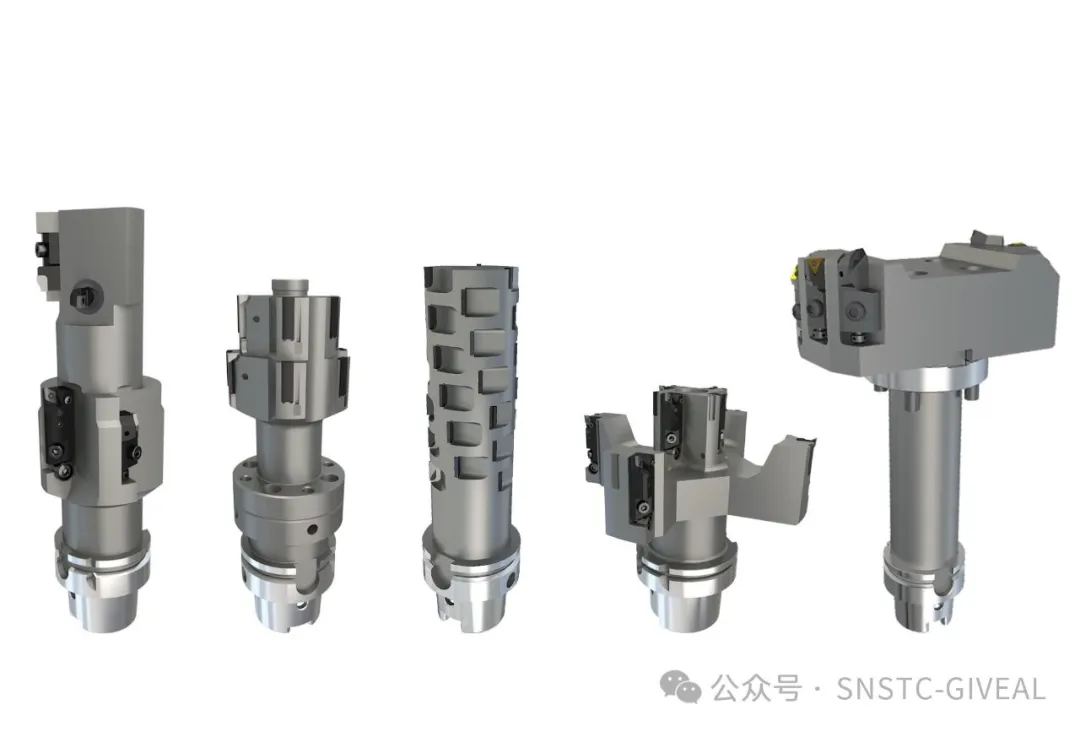